Press Forming
high performance press (superior equipment)
= high quality and precisely formed products
(superior products)
Here at Nishimura, progressive press forming using rigid and reliable presses, and digital controlled press forming with high-precision servo presses, are performed. Precision stamping tools for press forming are made in-house, which reflects our commitment to the utmost precision. These efforts have helped us produce excellent and reliable products such as metal separators for fuel cells and electronic components, which are enjoying significant reputation from customers from home and overseas. Metal separators for fuel cells are made of so-called "hard-to-form" material, such as stainless steel and titanium. We've been undertaking extensive technical development, to make press forming of these challenging materials possible.
Special, high-performance presses we can rely on
-
Press Multi-link motion high-speed press Manufacturer Yamada Dobby Model MXM-80L Bed Size 1500×800 SPM 400 Capacity 80 tons -
Press Direct drive digital servo press Manufacturer Hoden Seimitsu Kako Kenkyusho Model MPS8400DS Bed Size 1800×800 Capacity 400 tons -
Press Highly-rigid servo press Manufacturer Amada Model SDE-3030SF Bed Size 1380×900 Capacity 300 tons
Click below for our other press machines.
View Our EquipmentNishimura's press forming technology from test stamping to mass production
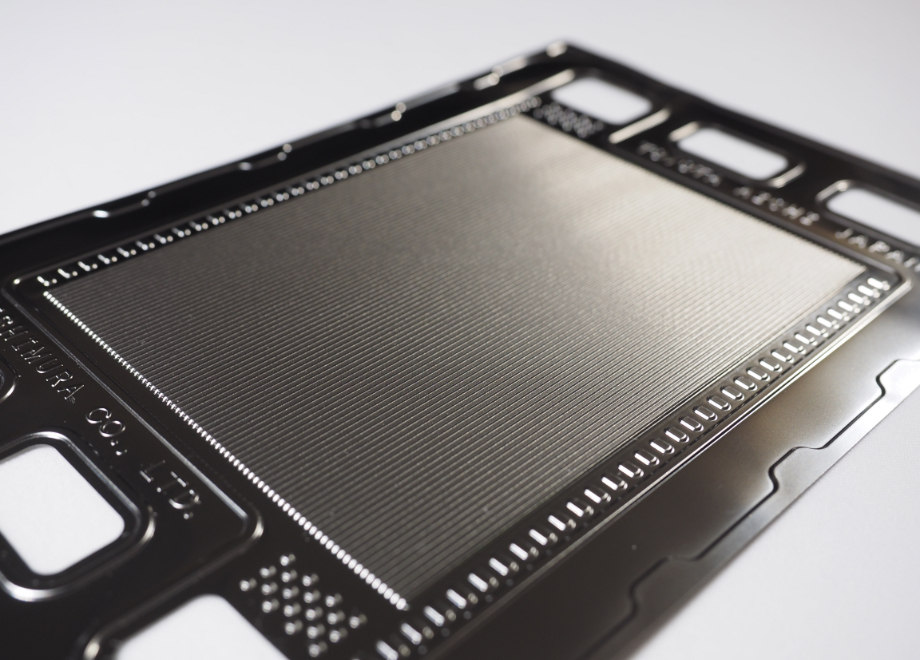
Our press forming technology will meet and exceed your expectations, in avoiding dull edges, press-forming of modified cross-section shape material, and forming of fine-pitch and higher-wall corrugated plates. Meanwhile, we know how to make maximum use of respective material's properties. With our high-precision dies, forming things that used to be impossible to form becomes possible. This facilitates integration of parts, and improves their performance.
Read more about our Die Design and ProductionPrecise punching of thick plates and cold forging processing
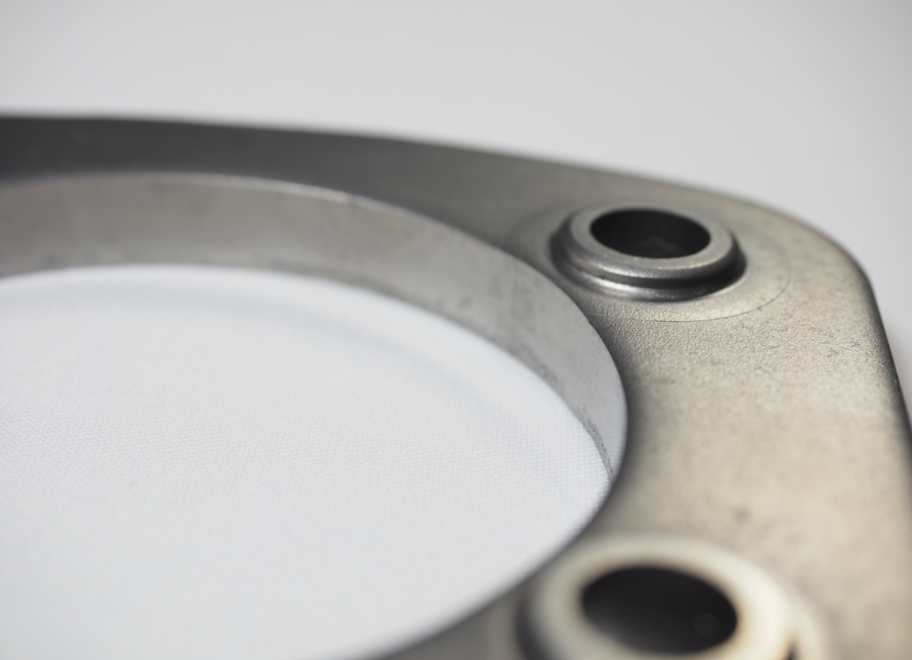
Exhaust system parts, for automobile industry
Plate thickness : 6.0mm
Material : S22C
Precision : precision of punched contour geometry: ±0.03mm
Accuracy of cold-forging formed geometry: ±0.05mm
Feature: achieved cold chick plate forging with high-precision dies and rigid press machine
Dealing with the most challenging shapes -- press-forming of micro module gears
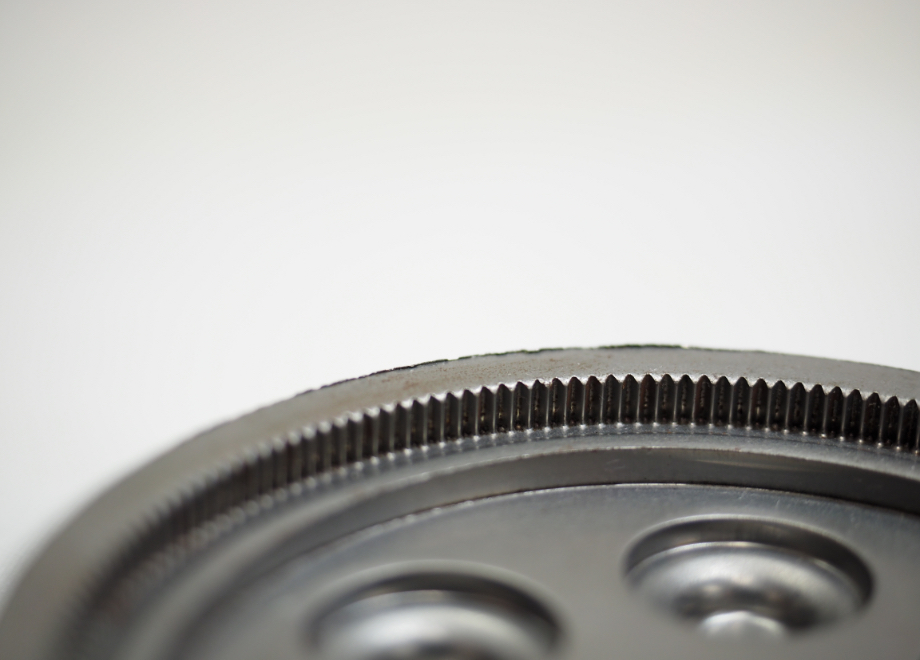
Seat recliner for vehicles
Plate thickness : 3.2mm
Material : S22C
Gear module : 0.28
Precision : precision of gear contour : ±0.02mm
Feature : precise press-forming of micro gear geometry. Appropriate management of clearance and adequate blade tip geometry prevent fracture of cross section and limit dull edges.
For more information on our works, click below.
View Our Works